Transactional certificates (also referred to as TC’s) are pivotal documents in the garment industry, especially in the context of sustainable supply chain management, since they are critical for ensuring the traceability and authenticity of products. In this article, we provide a comprehensive overview of the process and best practices for handling transactional certificates in relation to purchase orders in the garment industry. Moreover, we dive into how brands can manage their certificates on purchase order level with Vintly.
Understanding Transactional Certificates
Transactional certificates are formal documents used to verify that the products in a shipment comply with specific standards or criteria. In the sustainable garment industry, these certificates often attest to the environmental and social standards of the production of goods, such as organic or fair-trade certifications. The use of these certificates is integral in maintaining transparency and trust in the supply chain, ensuring that the products meet required sustainability practices and compliance.
Application of TC’s within the Garment Industry
In the case of apparel and garments, supply chains are often complex as they tend to span across multiple countries with various raw material providers, suppliers and service providers involved. In this complex web of manufacturing and logistics, transactional certificates act as a guarantee that products have been produced and handled according to the claimed standards. This is particularly important in an era where consumers and regulators are increasingly demanding proof of sustainable practices. Below are some examples of how to work with and implement transactional certificate:
- Issuance at the Point of Origin: The process begins at the point of origin, where the producer or manufacturer must obtain a transactional certificate from a recognized certifying body. This certificate should be based on a thorough audit of the production processes and supply chain management practices.
- Incorporating Certificate Details in Purchase Orders: When a buyer, such as a retailer or distributor, places a purchase order, it's essential to specify the need for a transactional certificate. This requirement should be clearly mentioned in the purchase order agreement.
- Verification Upon Receipt: Upon receiving the shipment, the buyer must verify the transactional certificate. This involves checking the authenticity of the certificate, ensuring it matches the shipment details, and confirming that it complies with the standards specified in the purchase order.
- Record Keeping: It’s critical to maintain detailed records of all transactional certificates. These records should be easily accessible for audits, compliance checks, and potential future reference.
- Handling Discrepancies: If discrepancies are found between the certificate and the received goods, it’s important to address these immediately. This might involve contacting the supplier for clarification, conducting additional inspections, or, in severe cases, rejecting the shipment.
Best Practices in Managing Transactional Certificates
- Integrate with Supply Chain Management Systems: Utilize advanced supply chain management software to track and manage transactional certificates. Such a tool can facilitate real-time tracking and reduce the risk of mismanagement.
- Regular Audits and Compliance Checks: Conduct regular audits of your suppliers and perform random checks on transactional certificates to ensure ongoing compliance with your standards.
- Training and Awareness: Ensure that all staff involved in procurement and supply chain management are trained and aware of the importance of transactional certificates and how to manage these.
- Building Strong Supplier Relationships: Develop strong relationships with suppliers to ensure a mutual understanding of the importance of sustainable practices and the role of transactional certificates.
- Staying Updated with Industry Standards: As the standards for sustainable practices evolve, it's crucial to stay informed and update your processes accordingly.
Challenges and Solutions
One of the main challenges in handling transactional certificates is the potential for fraudulent documents. To mitigate this, companies should work with reputable certifying bodies and conduct thorough due diligence. Another challenge is the administrative burden of managing these certificates, where leveraging technology and automating parts of the process can significantly reduce this burden.
Vintly brings a dynamic flair to supply chain collaboration by uniting brands and suppliers on a single platform. This streamlines the management of purchase orders, right down to the nitty-gritty of certificates for each order. With Vintly's PO certificate feature, brands can effortlessly request certificates, both transactional and beyond, for each order, ensuring suppliers know exactly what's being requested and how to provide.
Handling multiple styles in one order that all require transactional certificates? Vintly allows users to assign multiple certificates to an order with ease.
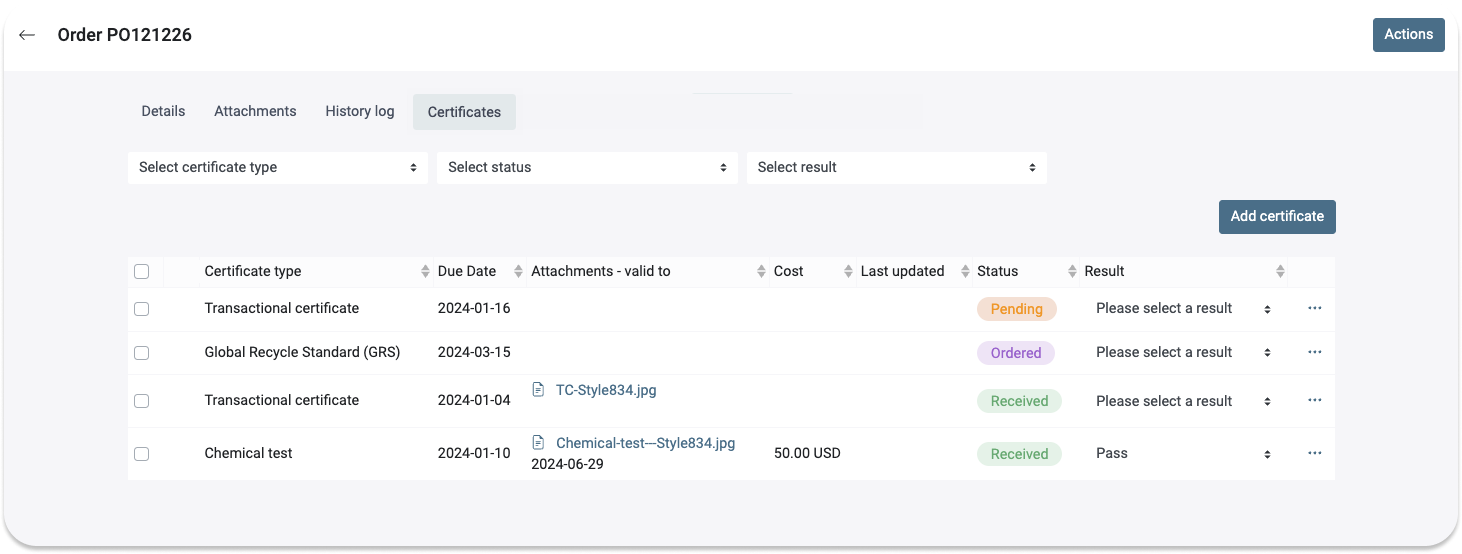
But Vintly isn't just about sending requests and collecting documents; it's about seamless tracking and follow-through. The platform's certificate feature gives each certificate a status, allowing users to monitor progress in real-time, aligned with their timelines.
Moreover, users get a bird's-eye view of all certificates and their statuses across all orders, ensuring nothing slips through the cracks. And the best part is that once certificates are uploaded to the purchase orders, they can be reviewed, approved, and remain easily accessible, even long after the order is received.
Vintly is redefining efficiency and clarity in supply chain management, one certificate at a time.
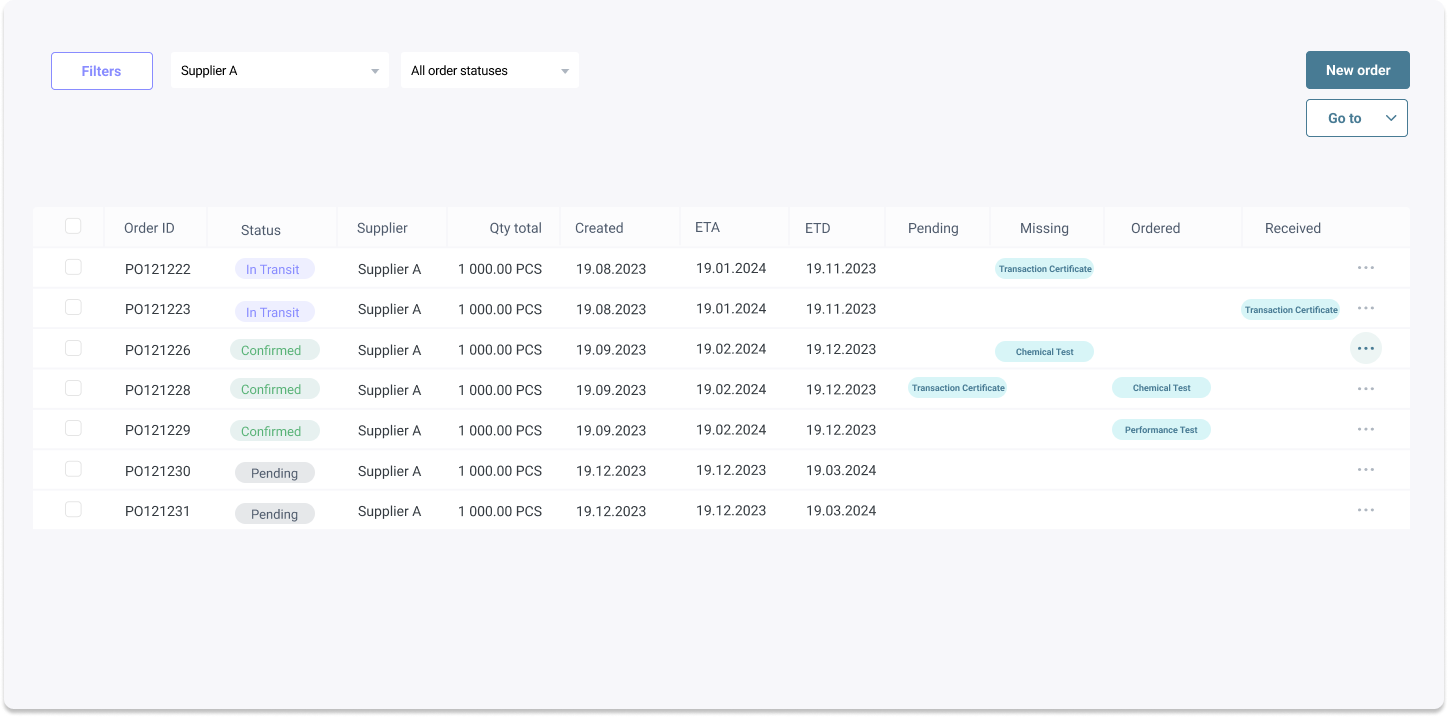
To Summarize
Transactional certificates play a crucial role in the sustainable garment industry, serving as a bridge between ethical production and informed purchasing. By understanding and implementing effective practices for handling these certificates, businesses can significantly contribute to a more transparent, accountable, and sustainable garment supply chain. The key lies in integrating these practices seamlessly into the existing supply chain processes, ensuring compliance without compromising on efficiency.
Interested to hear more? Get in touch with us.